Możliwości konstrukcyjne betonu zbrojonego stalą osiągają swój szczyt w technologii betonu sprężonego, gdzie odpowiednio ułożone i naprężone cięgna zastępują tradycyjne pręty zbrojeniowe. Od listopada 2016 roku Zakład Prefabrykacji Buszrem w Sochaczewie dostarcza swoje produkty strunobetonowe na kolejne inwestycje.
Prefabrykacja na nowo
Pewne technologie budowlane budzą (zwłaszcza u ludzi nie związanych z tą branżą) konkretne i najczęściej bardzo mocne skojarzenia. Tak jest na przykład z prefabrykacją, przy czym akurat w tym wypadku nie są to skojarzenia pozytywne - to raczej wizje marnie wykonanych i kiepsko spasowanych bloków z tzw. "wielkiej płyty" powstających w Polsce do początku lat dziewięćdziesiątych XX wieku. Mało kto uświadamia sobie, że prefabrykacja jest doskonałą metodą szybkiej i precyzyjnej produkcji elementów budowlanych. Na przykład słupów. Ogromnym jej plusem jest chociażby fakt, że komponenty wykonuje się nie na placu budowy, ale w niemal laboratoryjnych warunkach fabrycznych, co znakomicie ułatwia otrzymanie zarówno reżimu wymiarowego o tolerancjach na budowie nieosiągalnych, jak i chociażby parametrów estetycznych. Przy odpowiednio przeprowadzonej prefabrykacji elementów betonowych otrzymać można jednolitą kolorystycznie powierzchnię (przy czym na wybór koloru również mamy wpływ), o równych krawędziach, niemal lustrzanej gładkości i jednolitej strukturze. Jednocześnie elementy te mogą być wykonywane niemal w dowolnym czasie i przywiezione na plac budowy wtedy, kiedy to potrzebne. Z punktu widzenia inwestycji cała operacja z wielu dni lub nawet tygodni żmudnego zbrojenia, szalowania, zalewania i wreszcie cierpliwego czekania na uzyskanie nośności - ogranicza się do niemal błyskawicznego montażu elementów.
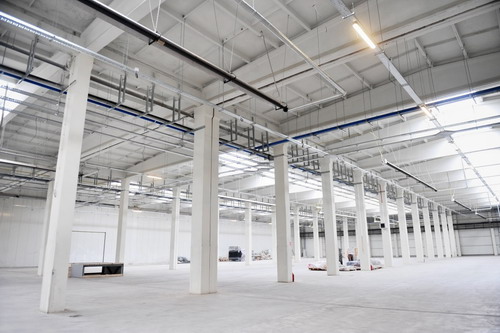
Beton sprężony jest bardziej wytrzymały od żelbetu
Pierwsza realizacja Buszrem z elementami strunobetonowymi
Obiekt: Hala magazynowa, zaplecze socjalne, łącznik w miejscowości Cielądz
Inwestor: HERCO Sp. z o.o.
Podstawowe parametry budynków:
układ bryły: prosty, zwarty,
liczba kondygnacji nadziemnych hala i łącznik: 1
technologia wykonawstwa hali i łącznika: stalowa, lekka obudowa
wysokość budynku hali : 12,00m
pow. zabudowy hali: 1 899,13 m2
kubatura łącznie: 23 845 m3
Żelbet
Kolejny przykład terminu budzącego mocne skojarzenia to beton (lub też w wypadku nieco lepiej poinformowanych - żelbet). Pierwszy obraz który przychodzi na myśl większości z nas - to szary, chropowaty, nieco brutalny w odbiorze materiał konstrukcyjny. Już różnica między betonem a żelbetem bywa trudna do wytłumaczenia, spora jednak część zapytanych odpowie prawdopodobnie, że chodzi o wzmocnienie betonu stalą. I w zasadzie sedno problemu zostanie uchwycone. Beton jako materiał "lubi" być ściskany. Jego wytrzymałość na taki rodzaj naprężeń jest ogromna. Gorzej sprawa się ma z rozciąganiem i zginaniem. Tutaj czysty beton wypada dość blado. Stąd też pomysł, aby partie elementów betonowych narażone na te rodzaje obciążeń wzmocnić odpowiednimi stalowymi prętami. Stal z kolei doskonale znosi zarówno rozciąganie jak i obciążenia zginające. Tak oto stworzyliśmy żelbet, W zasadzie nie my i nawet nie nasi rodzice - pomysł jest bowiem dość stary. Czy można nowocześniej? Można.
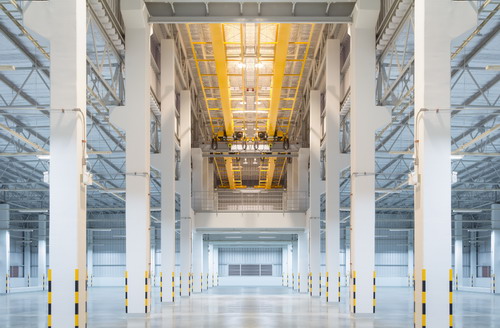
Zakład Prefabrykacji Buszrem produkuje również słupy z betonu sprężonego
Konstrukcję dachu hali Herco stanowią kratowe dźwigary stalowe (stal profilowa St3S) wsparte na prefabrykowanych słupach żelbetowych produkcji Buszrem. Słupy żelbetowe sprężone w rozstawie głównym co 6m. Wewnętrzne o wymiarach 40cm x 50cm oraz zewnętrzne o wymiarach 40cm x 40cm.
Nowoczesność, czyli beton sprężony
Skoro beton "lubi" być ściskany - to może spróbować go "wewnętrznie" ścisnąć? A mówiąc bardziej technicznie - wprowadzić do elementów betonowych niejako wewnętrznie wprogramowane naprężenia ściskające, które będą równoważyć przynajmniej w części działające na belkę czy słup siły dla tego materiału niekorzystne?
Wymyśliliśmy właśnie beton sprężony. (No dobrze, wymyślilibyśmy gdyby ktoś tego nie zrobił pół wieku temu). Doskonały materiał o wytrzymałości zdecydowanie większej niż klasyczny żelbet. Można więc przekryć większe rozpiętości, ustawić wyższe i smuklejsze słupy, zaoszczędzić miejsce, materiał i koszty transportu. Dodatkowo jest to materiał całkowicie szczelny i odporny na spękania. Wytrzymałość na ściskanie która w wypadku żelbetu wynosiła maksymalnie 60 MPa, a z reguły jednak bliżej 30 MPa - wzrasta nawet do 100 MPa. Maksymalne rozpiętości elementów przestają w zasadzie być dyktowane właściwościami materiału, głównym ograniczeniem stają się możliwości transportowe. W końcu przewiezienie belek o długości ponad 40m z fabryki na plac budowy to już poważna operacja logistyczna. Mimo to - beton sprężony wydaje się niezastąpiony chociażby przy budowie mostów czy wiaduktów, ale także na przykład hal przemysłowych. Cały problem w tym właśnie, że takich elementów nie można już wykonać na budowie.
Odpowiednie ułożenie i naprężenie cięgien (które w betonie sprężonym zastąpią tradycyjne pręty zbrojeniowe) wymaga bardzo nowoczesnego zakładu produkcyjnego, doświadczonych inżynierów produkcji i projektantów. Tu wracamy do opisanej na początku prefabrykacji. Oczywistym jest, że przy takich elementach staje się ona niezbędna. Warto jednak zauważyć, że jest także bardzo korzystna. Wykonanie kilku czy kilkunastu jednakowych słupów mających stanowić podparcie dachu hali fabrycznej może dzięki temu nastąpić niemal na linii produkcyjnej z użyciem tych samych form i maszyn. Może również trwać niezależnie od etapu na którym znajduje się budowa, a także od warunków atmosferycznych czy pory roku. Co istotniejsze - ich produkcja może rozpocząć się długo przed uzyskaniem decyzji o pozwoleniu na budowę. Wykonane elementy spokojnie mogą zaczekać na montaż w fabrycznym magazynie. Wreszcie - słupy o wysokości niemal 12m i przekroju 40x40 cm stają się czymś zupełnie naturalnym. Dodać należy, że przy użyciu tradycyjnej technologii żelbetowej byłoby to zdecydowanie bliżej nurtu science - fiction.
Źródło i zdjęcia: Buszrem