The French capital is one interesting silhouette richer: The new 171 meter high Tour D2 in the western Paris quarter of La Defense is ready. In a construction period of only 12 months the 37 stories of the concrete structural work have risen up into the air. An ambitious project, whose successful and punctual execution is due not least to the use of tailor-made SCF self-climbing formwork made by Hünnebeck.

Interesting silhouette: The new 171 meter high Tour D2 in the western Paris quarter of La Defense
Foto. Copyright: Vinci Construction
Europe’s largest high-rise district, La Defense in Paris, has been under reconstruction since 2006. Some of the gigantic office towers are being refurbished, some torn down and rebuilt. For example, the Tour Veritas had to make way for the new Tour D2. During its design, the two architects Anthony Béchu and Tom Sheehan focused on organic shapes and structures. On an oval ground plan there is an almost 180 meter high glass body crowned by a dome. The rounded facade of the glass body is more reminiscent of an exotic plant than a technical structure.
Not only the appearance, but also the supporting structure of the building has caused a stir in the industry. Although the main load rests on the massive, oval concrete core of the tower, the facade also takes up a considerable share. Steel girders arranged in a V shape, which introduce part of the load into the core of the building via steel structures in the floor slab, are used for this. As a result, columns are superfluous, which are usually used to take up the vertical loads of the slabs.
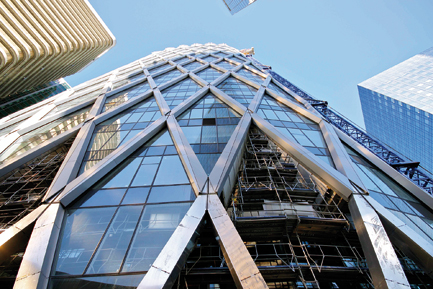
Although the main load rests on the massive, oval concrete core of the tower, the facade also takes up a considerable share
Foto. Copyright: Vinci Construction
The Vinci Construction company was responsible for the punctual building of the shell construction. The formwork for the unusual building was supplied by Hünnebeck.
The key element of the formwork concept was the modular self-climbing formwork SCF, which ensured the rapid and safe production of the oval concrete core. Because the brackets of this formwork device provide an unusually high vertical load-bearing capacity of up to 150 kN, it is possible to produce large platform widths – ensuring efficiency and safety.
Tailor-made Formwork Concept
The tailor-made formwork concept was designed by Hünnebeck France together with the German SCF specialists in Ratingen. This comprised all of the formwork solutions for the walls and slabs of the building core, as well as the five basement stories. The concept was implemented on a multinational basis: the overall concept, the self-climbing technology and the designs of the special steel parts of the climbing platforms came from Germany. The manufacturing drawings were drawn up by Hünnebeck engineers in the Czech Republic, while the French company planned and implemented the formwork concept. The materials and systems used – 500 t overall – came from Germany, Poland, France and Dubai. These were delivered on time to the Hünnbeck branch office in Mitry-Mory to the north of Paris, from where they were transported just-in-time to the construction site.
Five Day Cycle
The SFC formwork used at Tour D2 consisted of 58 brackets. The 25 SCF platforms built from these consisted of five to six (in some cases) working and finishing platforms in each case. With this formwork device it was possible to complete one story consisting of more than 2,000 m2 of formwork surface in a five-day cycle:
Day 1: The completely enclosed platforms climbed along the external walls of the core. Immediately afterwards the external formwork suspended on crane trolleys in the windproof enclosed area were closed and aligned by hand. Depending on the type of wall, this was either Manto formwork or specifically designed wooden beam wall formwork for the slightly rounded shapes in the fair-faced concrete quality SB 4.
On days 2 and 3 the reinforcement cages of the exterior walls were delivered and installed. Here, the builders of the shell construction used the upper stages of the interior platforms which had not yet been climbed as a working surface – one particular advantage of the SCF concept. The reason for this is that the entire installation of the reinforcement was carried out from free platforms which offered the team sufficient space and therefore also a high level of safety for their work.
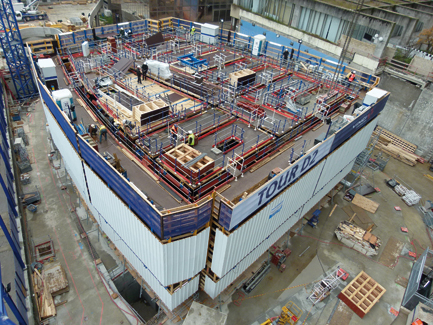
The tailor-made formwork concept comprised all of the formwork solutions for walls, slabs and the five basement stories
Foto. Copyright: Hünnebeck
On the second day of the cycle the builders of the shell construction also began to produce the formwork of the supporting interior walls, for example, for the elevator shaft or the slightly wave-shaped central corridor which runs through the core. On the third day they installed the reinforcement cages of the remaining interior walls. Here too, they used the highest stage of the interior platforms that had not yet been climbed as a working surface.
The fourth day was used for closing and aligning all of the formwork, as well as the installation of the formwork ties. On the fifth day the walls were then concreted. For this, a free-flowing, self-compacting concrete was used, which was introduced without shaking. Its particular properties (including a small grading curve) ensured that the highly reinforced components were completely penetrated. At the same time, these properties made it possible to comply with the required fair-faced concrete class (SB4).
Two floors below the highest working level, some trailing interior walls were erected at the same time - also with Manto formwork. Two floors below this again, the slabs were produced within and outside the core. Within the core, light Topec frame panels made of aluminum were used. The slabs outside the core were concreted on trapezoidal metal sheets. These are attached to the steel girders for connecting the external facade and remain permanently within the building.
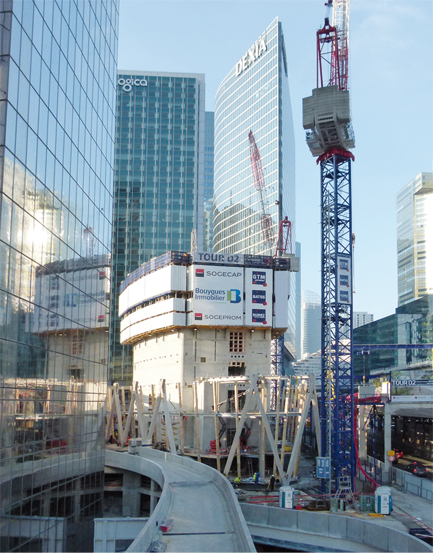
The modular self-climbing formwork SCF ensured fast and efficient production of the oval concrete core without a crane
Foto. Copyright: Hünnebeck
Successful Project
“In this project we had to find detailed solutions to many challenges relating to formwork technology,” sums up Guillaume le Boubennec, Director of Project Services at Hünnebeck France. “But our self-climbing SCF as a base unit allowed us every freedom to solve all of the challenges in an extremely flexible manner and enabled the construction site to work quickly and smoothly.”
Źródło: Świat Betonu, nr 1-2 (7) 2015